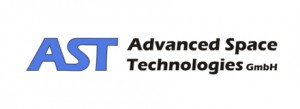
Company | Advanced Space Technologies GmbH |
Contact | Dr. Hans-Peter Harmann |
harmann@advancedspacetechnologies.de | |
Address | Zeppelinstraße 9b D-28816 Stuhr |
Country | ![]() |
Phone | +49 (421) 871 821 51 |
AST Advanced Space Technologies GmbH
Basic entry – no further information available
Unsere Kompetenz in einem Satz
Produkte und Dienstleistungen sowie Forschung und Entwicklung
Besondere Infrastruktur und Anlagen
Zertifizierung
––– Bitte zuliefern –––
Beispiele von Kunden
Missionen
AST
The PSU is a unique power supply system, for supplying power to the panchromatic band camera and the multispectral camera. It has 24 precise power outputs, as well as a TC/TM interface and regulated heater outputs. The power supply consists of a total of 8 individually designed, manufactured and tested modules.
The AEU supplies power to both the "normal" cameras (N-AEU) and the "fast" cameras (F-AEU). The N-AEU consists of 6 sophisticated power supply modules, 2 command and control modules, and an internal supply module. The F-AEU consists of 1 sophisticated power supply module, 2 command and control modules, and 1 internal supply module.

HTV assists in the planning and execution of electrical tests and physical analyses.
The aim is to investigate the effectiveness of board/unit level testing compared to traditional EEE level testing.
Started: 17.05.2021
The objective of this study is to present, by means of research and questionnaires, the share of Germany and other nations in space-qualified EEE components and the reasons for the (uneven) distribution.
This research is part of the INNOspace® initiative and the Space2Motion network.
From 01.01.2021 until 31.08.2021.
Short-Presentation (in German)

More than 5500 individual electronic components as well as complete printed circuit boards were extensively tested and examined at HTV with regard to weak points, to ensure that all components work properly and in the long term during the more than ten-year mission of the comet "Rosetta" under the extreme conditions in space.
Scientific magnetometer (JAMG IS),
JANUS: Optical head unit heater control,
JANUS: soldering of sensor electronics.
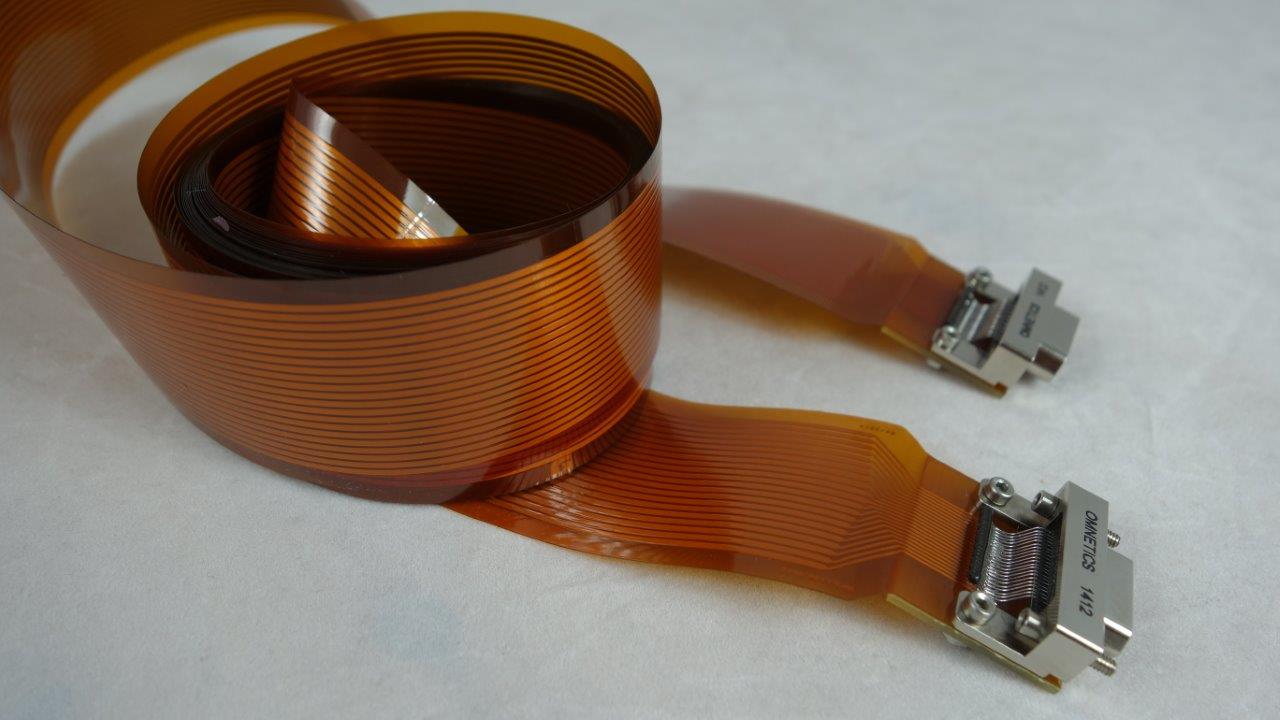
HP3 Electronics development and manufacturing,
Radiometer Electronics development and manufacturing,
Design of >5m Long Flex PCBs.
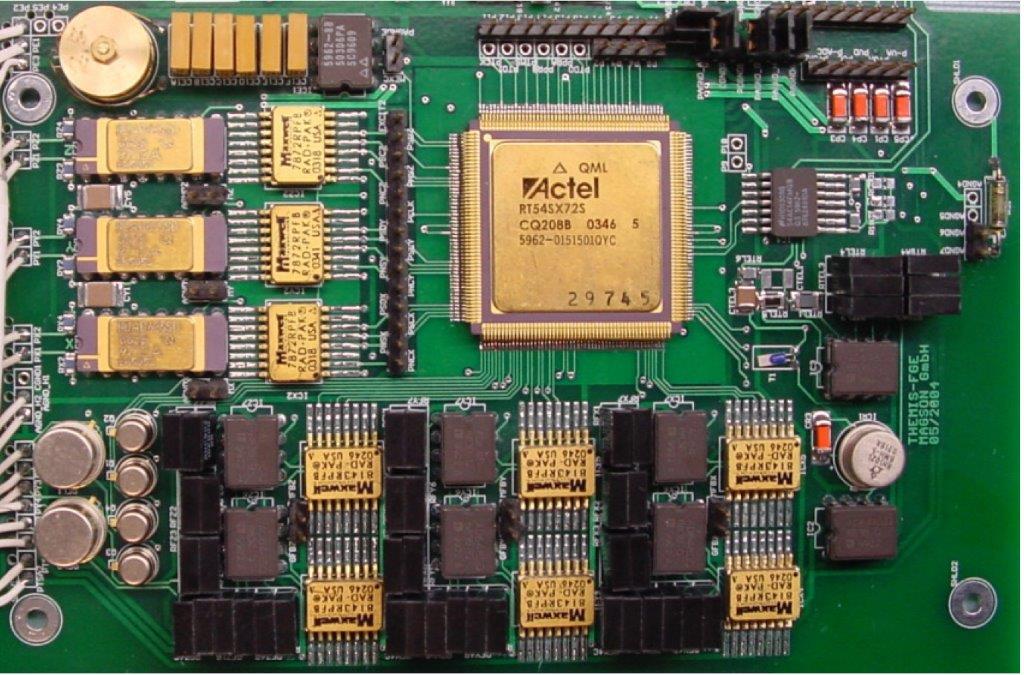
Electronics development of first magnetometer utilizing a self-developed RISC processor.
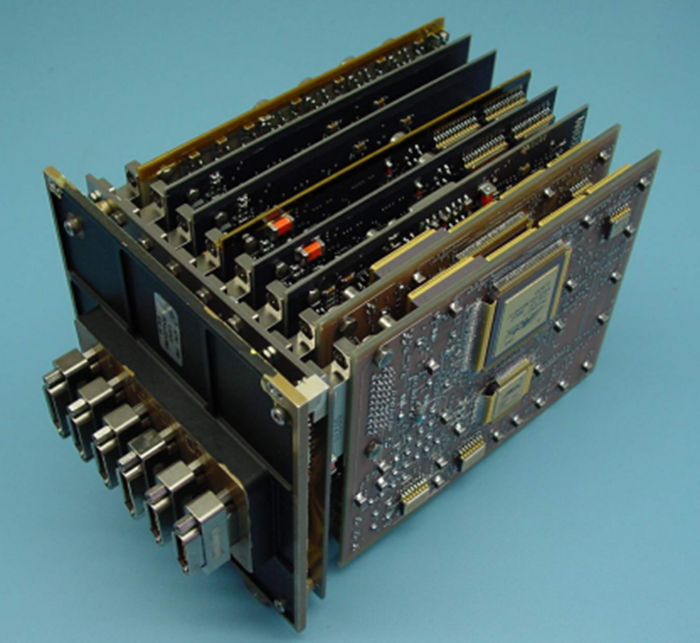
Magnetometer electronics
Landing gear electronics
Anchor system electronics
Thermal control system electronics
PCB Layouts for board computer
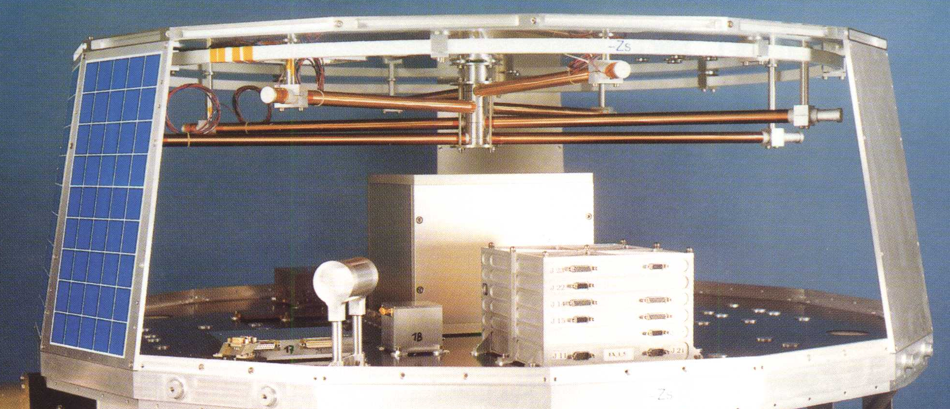
Magnetometer -magnet torquers system to accerlerate the satellite spin rate from 1rpm to 60rpm after deployment.
Electronics development and manufacturing of a IR spectrometer calibration source
Electronics development and manufacturing of Magson´s first digital space magnetometer with near-sensor signal digitalization.
Precision mechanics for electronic housings, mechanisms, optical instruments and structures
Precision mechanics for electronic housings, mechanisms, optical instruments and structures
Precision mechanics for electronic housings, mechanisms, optical instruments and structures
Hardware for HF modules
Precision mechanics for electronic housings, mechanisms, optical instruments and structures
Hardware for HF modules
Precision mechanics for electronic housings, mechanisms, optical instruments and structures
Precision mechanics for electronic housings, mechanisms, optical instruments and structures
Precision mechanics for electronic housings, mechanisms, optical instruments and structures
Precision mechanics for electronic housings, mechanisms, optical instruments and structures
Precision mechanics for electronic housings, mechanisms, optical instruments and structures
Precision mechanics for electronic housings, mechanisms, optical instruments and structures
Precision mechanics for electronic housings, mechanisms, optical instruments and structures
Precision mechanics for electronic housings, mechanisms, optical instruments and structures
Precision mechanics for electronic housings, mechanisms, optical instruments and structures
Precision mechanics for electronic housings, mechanisms, optical instruments and structures
Precision mechanics for electronic housings, mechanisms, optical instruments and structures
Precision mechanics for electronic housings, mechanisms, optical instruments and structures
Precision mechanics for electronic housings, mechanisms, optical instruments and structures
Precision mechanics for electronic housings, mechanisms, optical instruments and structures
Precision mechanics for electronic housings, mechanisms, optical instruments and structures
Precision mechanics for electronic housings, mechanisms, optical instruments and structures
Precision mechanics for electronic housings, mechanisms, optical instruments and structures
Precision mechanics for electronic housings, mechanisms, optical instruments and structures
Precision mechanics for electronic housings, mechanisms, optical instruments and structures
Precision mechanics for electronic housings, mechanisms, optical instruments and structures
Precision mechanics for electronic housings, mechanisms, optical instruments and structures
Precision mechanics for electronic housings, mechanisms, optical instruments and structures
Precision mechanics for electronic housings, mechanisms, optical instruments and structures
Precision mechanics for electronic housings, mechanisms, optical instruments and structures
Precision mechanics for electronic housings, mechanisms, optical instruments and structures
Precision mechanics for electronic housings, mechanisms, optical instruments and structures
Precision mechanics for electronic housings, mechanisms, optical instruments and structures
Precision mechanics for electronic housings, mechanisms, optical instruments and structures
Precision mechanics for electronic housings, mechanisms, optical instruments and structures
Sheet metal structures for MLI support
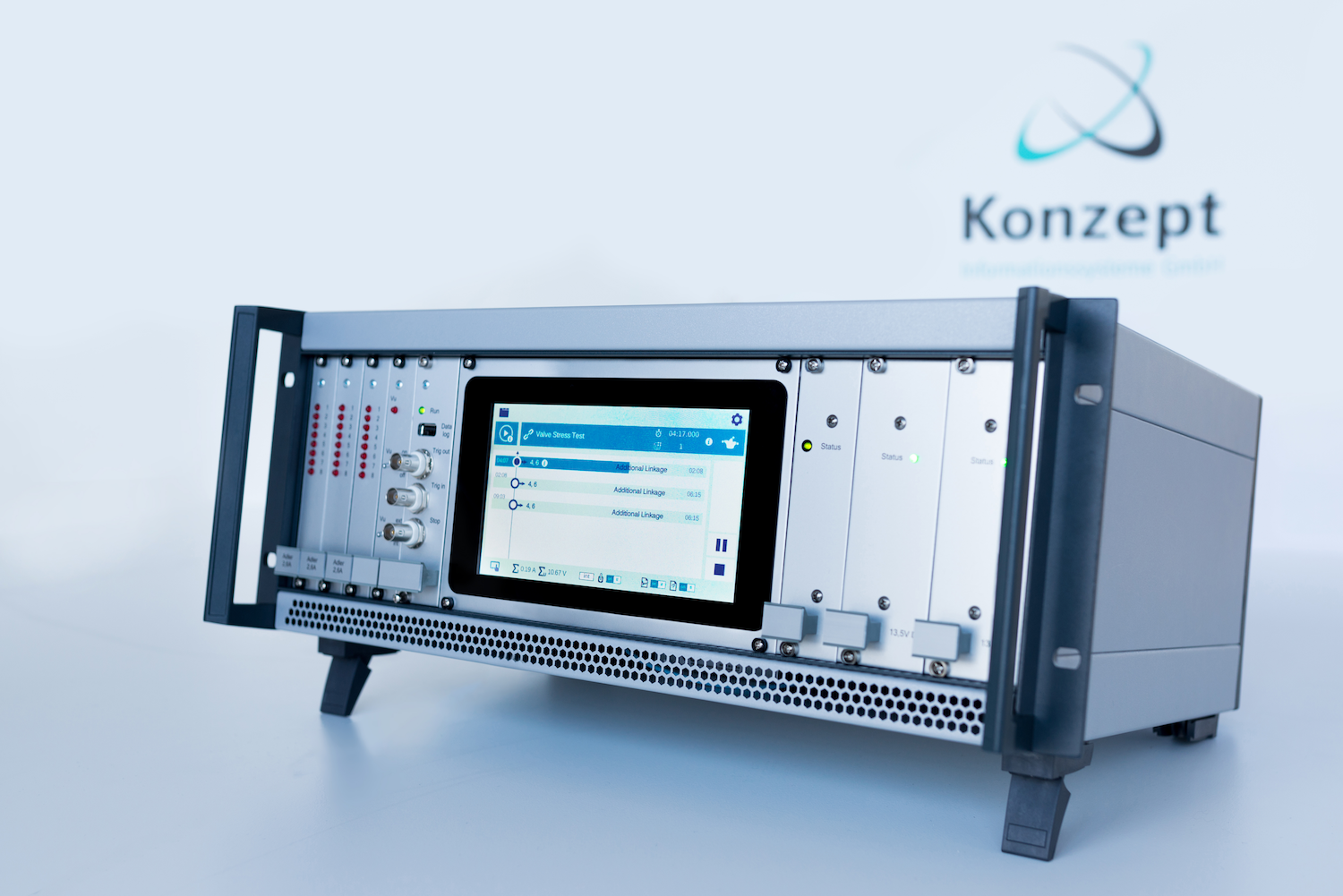
The Programmable Digital Current Regulator (DCR) allows to control the output current for different applications with high flexibility. Execution and control parameters can be defined unsing an intuitve operator interface and menu structure. The DCR will deliver the appropriate current curve for the indiviual current curve based on the defined parameters.
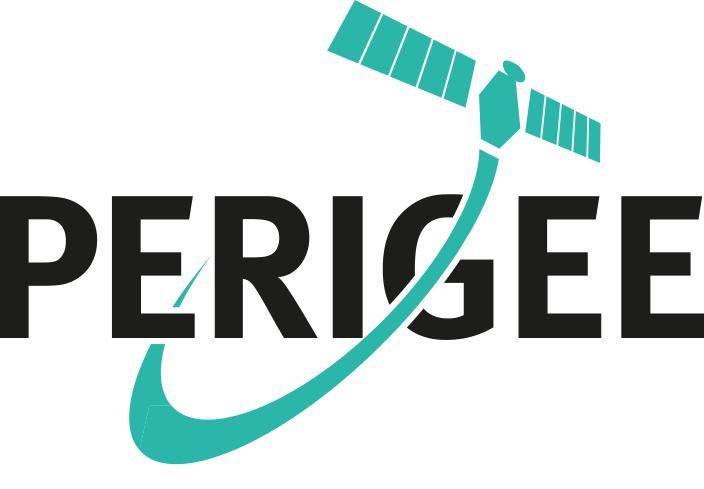
The desktop application PERIGEE has been developt for the high and complex requirements of space missions and helps project teams to cope with the high degree of complexity through the usage of modern UI concepts. Within short time the communication both among satellite components and between satellite and ground can be defined by using ECSS-E-ST-70-41C (PUS-C).
- Software Verification
- Board Level Testing for On-Board Mass Memory Unit (MMU)
- Unit Testing of a performance analysis tool of the navigation system
- Development of a data extractor for NetCDF files
- Validation of On-Board Computer
- Functional Verification of the Data Handling Systems (DHS)
- Check-Out & FV
- Development of Central Software Modules
- Unit Testing
- EFM/PFM RTE Bench Commisionin
Development of UI components and tools for the Mission Operation Center (MOC)
- Development of the On-Board Computer Simulators
- Development of RTS modules
- Check-Out & FV
- Test Management for Validation of Onboard Software und Real-Time Simulator
- Support of OBSW IST
- Functional Verification of the Drag Free Attitude Control Systems (DFACS)
- Entwicklung von Softwaremodulen für die Real-Time Simulator (RTS) Umgebung
- Development of SCOE Software for Instrument Simulator
- Development of a Source Packet Analyser
Front-End (UI) Development of the video data management system for the Electromagnetic Levitator (EML) in the Microgravity User Support Centre (MUSC)
Development of the On-Board Software Prototype "Controller for autonomous Space Systems (KARS)"
Development of Software Modules for the Real-Time Simulator (RTS) Environment
Development of Software Modules and Drivers for the Real-Time Simulator (RTS) Environment
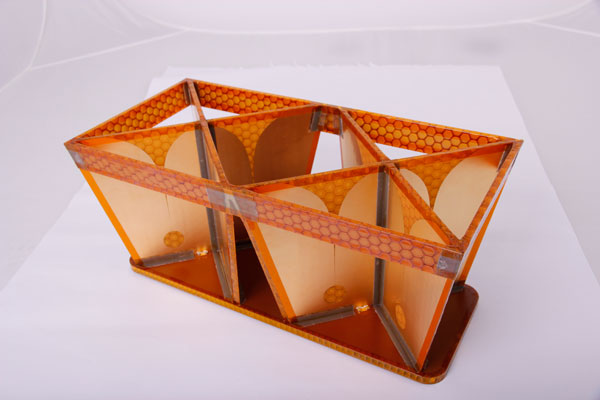
The actual antenna geometry (copper) is introduced after the laminate manufacturing by etching.
- Development of agile antenna frontends and components for mobile satellite communication
- HF- distributor networs and HF-components for satellite payloads
Precision mechanics for electronic housings, mechanisms, optical instruments and structures
Precision mechanics for electronic housings, mechanisms, optical instruments and structures
- Support of SVT, OST and SFT of the Data Handling System (DHS)
- Development of Payload Controllers in Central Software (CSW)
- QA and Unit Testing for CSW and MMUF software
- Development of Tools for AIT and Check-Out
ASP-Equipment entwickelt und fertigt eine flüssigkeitsgekühlte Power Supply Unit für ein ultragenaues Elektronenstrahlmikroskop mit Anbindung an einen CAN Bus. Die Leistung beträgt 1500W. Zahlreiche Ausgangsspannungen bis 20.000V.
ASP-Equipment entwickelt und produziert High Power Amplifier für das Bodensegment im Ku Band, DBS Band und Tri-Band (C, X, Ku) .
Entwicklung eines ITAR freien autarken Batteriemangementsystem (BMS). Das BMS wird heute in Stückzahlen von etwa 50 Einheiten pro Jahr exklusiv an einen namhaften europäischen Hersteller für Raumfahrtbatterien geliefert.
ASP-Equipment entwickelt und produziert High Power Amplifier für das Bodensegment im Ku Band, DBS Band und Tri-Band (C, X, Ku).
ASP-Equipment entwickelt und produziert DC/DC Converter für Sternsensoren als Produkt in Stückzahlen von etwa 40 Stück pro Jahr für einen führenden deutschen Ausrüstungshersteller.
ASP-Equipment entwickelt und fertigt einen Hochleistungskonverter für die Energieversorgung in Luftfahrzeugen für Brennstoffzellen bis 150.000W.
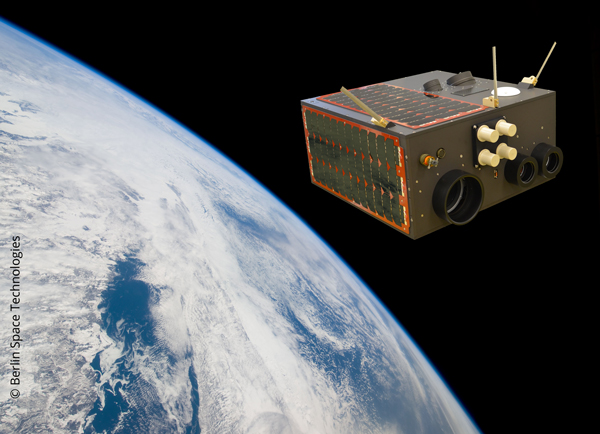
Test environment for in orbit verification of Point-of-Load voltage converter based on the SPPL12420RH chip
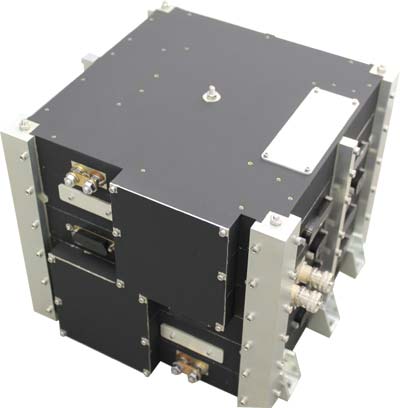
- Receiving, formatting and storing of science data
- Instrument Control
The Magnetometer is an instrument for measuring three-dimensional magnetic fields. It is based on the fluxgate principle, using three independent ring-core sensor heads for each orthogonal axis.
The Magnetometer is an instrument for measuring three-dimensional magnetic fields. It is based on the fluxgate principle, using three independent ring-core sensor heads for each orthogonal axis.
The Magnetometer is an instrument for measuring three-dimensional magnetic fields. It is based on the fluxgate principle, using three independent ring-core sensor heads for each orthogonal axis.
The Magnetometer is an instrument for measuring three-dimensional magnetic fields. It is based on the fluxgate principle, using three independent ring-core sensor heads for each orthogonal axis.
The Magnetometer is an instrument for measuring three-dimensional magnetic fields. It is based on the fluxgate principle, using three independent ring-core sensor heads for each orthogonal axis.
The Magnetometer is an instrument for measuring three-dimensional magnetic fields. It is based on the fluxgate principle, using three independent ring-core sensor heads for each orthogonal axis.
The Magnetometer is an instrument for measuring three-dimensional magnetic fields. It is based on the fluxgate principle, using three independent ring-core sensor heads for each orthogonal axis.
The Magnetometer is an instrument for measuring three-dimensional magnetic fields. It is based on the fluxgate principle, using three independent ring-core sensor heads for each orthogonal axis.
The Magnetometer is an instrument for measuring three-dimensional magnetic fields. It is based on the fluxgate principle, using three independent ring-core sensor heads for each orthogonal axis.
The Magnetometer is an instrument for measuring three-dimensional magnetic fields. It is based on the fluxgate principle, using three independent ring-core sensor heads for each orthogonal axis.
The Magnetometer is an instrument for measuring three-dimensional magnetic fields. It is based on the fluxgate principle, using three independent ring-core sensor heads for each orthogonal axis.
The Magnetometer is an instrument for measuring three-dimensional magnetic fields. It is based on the fluxgate principle, using three independent ring-core sensor heads for each orthogonal axis.
The Magnetometer is an instrument for measuring three-dimensional magnetic fields. It is based on the fluxgate principle, using three independent ring-core sensor heads for each orthogonal axis.
The Magnetometer is an instrument for measuring three-dimensional magnetic fields. It is based on the fluxgate principle, using three independent ring-core sensor heads for each orthogonal axis.
The Magnetometer is an instrument for measuring three-dimensional magnetic fields. It is based on the fluxgate principle, using three independent ring-core sensor heads for each orthogonal axis.
The Magnetometer is an instrument for measuring three-dimensional magnetic fields. It is based on the fluxgate principle, using three independent ring-core sensor heads for each orthogonal axis.
The Magnetometer is an instrument for measuring three-dimensional magnetic fields. It is based on the fluxgate principle, using three independent ring-core sensor heads for each orthogonal axis.
The Magnetometer is an instrument for measuring three-dimensional magnetic fields. It is based on the fluxgate principle, using three independent ring-core sensor heads for each orthogonal axis.
The Magnetometer is an instrument for measuring three-dimensional magnetic fields. It is based on the fluxgate principle, using three independent ring-core sensor heads for each orthogonal axis.
The Magnetometer is an instrument for measuring three-dimensional magnetic fields. It is based on the fluxgate principle, using three independent ring-core sensor heads for each orthogonal axis.
The Magnetometer is an instrument for measuring three-dimensional magnetic fields. It is based on the fluxgate principle, using three independent ring-core sensor heads for each orthogonal axis.
These devices interact with the Earth’s magnetic field and create control torque, which can be adjusted to the required value. Combined with one or more reaction wheels, they provide all the control you need to maintain your spacecraft’s attitude, from low-Earth orbit up to geo-stationary orbit. And, unlike thrusters, torquers do not need valuable consumables, are low power components and high reliable.
These devices interact with the Earth’s magnetic field and create control torque, which can be adjusted to the required value. Combined with one or more reaction wheels, they provide all the control you need to maintain your spacecraft’s attitude, from low-Earth orbit up to geo-stationary orbit. And, unlike thrusters, torquers do not need valuable consumables, are low power components and high reliable.
These devices interact with the Earth’s magnetic field and create control torque, which can be adjusted to the required value. Combined with one or more reaction wheels, they provide all the control you need to maintain your spacecraft’s attitude, from low-Earth orbit up to geo-stationary orbit. And, unlike thrusters, torquers do not need valuable consumables, are low power components and high reliable.
These devices interact with the Earth’s magnetic field and create control torque, which can be adjusted to the required value. Combined with one or more reaction wheels, they provide all the control you need to maintain your spacecraft’s attitude, from low-Earth orbit up to geo-stationary orbit. And, unlike thrusters, torquers do not need valuable consumables, are low power components and high reliable.
These devices interact with the Earth’s magnetic field and create control torque, which can be adjusted to the required value. Combined with one or more reaction wheels, they provide all the control you need to maintain your spacecraft’s attitude, from low-Earth orbit up to geo-stationary orbit. And, unlike thrusters, torquers do not need valuable consumables, are low power components and high reliable.
These devices interact with the Earth’s magnetic field and create control torque, which can be adjusted to the required value. Combined with one or more reaction wheels, they provide all the control you need to maintain your spacecraft’s attitude, from low-Earth orbit up to geo-stationary orbit. And, unlike thrusters, torquers do not need valuable consumables, are low power components and high reliable.
These devices interact with the Earth’s magnetic field and create control torque, which can be adjusted to the required value. Combined with one or more reaction wheels, they provide all the control you need to maintain your spacecraft’s attitude, from low-Earth orbit up to geo-stationary orbit. And, unlike thrusters, torquers do not need valuable consumables, are low power components and high reliable.
These devices interact with the Earth’s magnetic field and create control torque, which can be adjusted to the required value. Combined with one or more reaction wheels, they provide all the control you need to maintain your spacecraft’s attitude, from low-Earth orbit up to geo-stationary orbit. And, unlike thrusters, torquers do not need valuable consumables, are low power components and high reliable.
These devices interact with the Earth’s magnetic field and create control torque, which can be adjusted to the required value. Combined with one or more reaction wheels, they provide all the control you need to maintain your spacecraft’s attitude, from low-Earth orbit up to geo-stationary orbit. And, unlike thrusters, torquers do not need valuable consumables, are low power components and high reliable.
These devices interact with the Earth’s magnetic field and create control torque, which can be adjusted to the required value. Combined with one or more reaction wheels, they provide all the control you need to maintain your spacecraft’s attitude, from low-Earth orbit up to geo-stationary orbit. And, unlike thrusters, torquers do not need valuable consumables, are low power components and high reliable.
These devices interact with the Earth’s magnetic field and create control torque, which can be adjusted to the required value. Combined with one or more reaction wheels, they provide all the control you need to maintain your spacecraft’s attitude, from low-Earth orbit up to geo-stationary orbit. And, unlike thrusters, torquers do not need valuable consumables, are low power components and high reliable.
These devices interact with the Earth’s magnetic field and create control torque, which can be adjusted to the required value. Combined with one or more reaction wheels, they provide all the control you need to maintain your spacecraft’s attitude, from low-Earth orbit up to geo-stationary orbit. And, unlike thrusters, torquers do not need valuable consumables, are low power components and high reliable.
These devices interact with the Earth’s magnetic field and create control torque, which can be adjusted to the required value. Combined with one or more reaction wheels, they provide all the control you need to maintain your spacecraft’s attitude, from low-Earth orbit up to geo-stationary orbit. And, unlike thrusters, torquers do not need valuable consumables, are low power components and high reliable.
These devices interact with the Earth’s magnetic field and create control torque, which can be adjusted to the required value. Combined with one or more reaction wheels, they provide all the control you need to maintain your spacecraft’s attitude, from low-Earth orbit up to geo-stationary orbit. And, unlike thrusters, torquers do not need valuable consumables, are low power components and high reliable.
These devices interact with the Earth’s magnetic field and create control torque, which can be adjusted to the required value. Combined with one or more reaction wheels, they provide all the control you need to maintain your spacecraft’s attitude, from low-Earth orbit up to geo-stationary orbit. And, unlike thrusters, torquers do not need valuable consumables, are low power components and high reliable.
These devices interact with the Earth’s magnetic field and create control torque, which can be adjusted to the required value. Combined with one or more reaction wheels, they provide all the control you need to maintain your spacecraft’s attitude, from low-Earth orbit up to geo-stationary orbit. And, unlike thrusters, torquers do not need valuable consumables, are low power components and high reliable.
These devices interact with the Earth’s magnetic field and create control torque, which can be adjusted to the required value. Combined with one or more reaction wheels, they provide all the control you need to maintain your spacecraft’s attitude, from low-Earth orbit up to geo-stationary orbit. And, unlike thrusters, torquers do not need valuable consumables, are low power components and high reliable.
These devices interact with the Earth’s magnetic field and create control torque, which can be adjusted to the required value. Combined with one or more reaction wheels, they provide all the control you need to maintain your spacecraft’s attitude, from low-Earth orbit up to geo-stationary orbit. And, unlike thrusters, torquers do not need valuable consumables, are low power components and high reliable.
These devices interact with the Earth’s magnetic field and create control torque, which can be adjusted to the required value. Combined with one or more reaction wheels, they provide all the control you need to maintain your spacecraft’s attitude, from low-Earth orbit up to geo-stationary orbit. And, unlike thrusters, torquers do not need valuable consumables, are low power components and high reliable.
These devices interact with the Earth’s magnetic field and create control torque, which can be adjusted to the required value. Combined with one or more reaction wheels, they provide all the control you need to maintain your spacecraft’s attitude, from low-Earth orbit up to geo-stationary orbit. And, unlike thrusters, torquers do not need valuable consumables, are low power components and high reliable.
These devices interact with the Earth’s magnetic field and create control torque, which can be adjusted to the required value. Combined with one or more reaction wheels, they provide all the control you need to maintain your spacecraft’s attitude, from low-Earth orbit up to geo-stationary orbit. And, unlike thrusters, torquers do not need valuable consumables, are low power components and high reliable.
Joint research project with:
Eureka: Sensor Technology, Telematics
DLR: Remote Sensing
University Würzburg: Pico-Satellites
Zentrum für Telematik e.V.: Satellite Network
Execution of RAMS (Reliability, Availability, Maintainability, Safety) Analysis with focus on hazard analysis and FMEA.
Plans for software develoment, verification and verification, CM, design
- Definition of test concepts: test / integration / work instructions, circuit plans
- First article inspections, acceptance tests
- Equipment safety files
- Operational Tests
- Generation of verification documents, verification at hardware
- RAMS calculations and analyses
- Integrated Logistic Support / Logistic Support Analysis (ILS/LSA) plans
- LORA, LCC
- Technical Documentation
Definition of Security Test Cases covering all security aspects on system level
Analysis of impact of security requirements, accreditatin, certificatin
Definition and execution of security test procedures
sensors and RFID Technology for automotive and aircraft industry
for high data rates, usable for various applications like first aid, journalsm, expeditions, military
Deployable Structure Subsystems
Lightweight CFRP Structures
Thermal Hardware
MLI
New Materials
Multilayer Insulations; HPS equipped the whole EDM Module inside and outside with MLI and will land with 10kg MLI on Martian surface
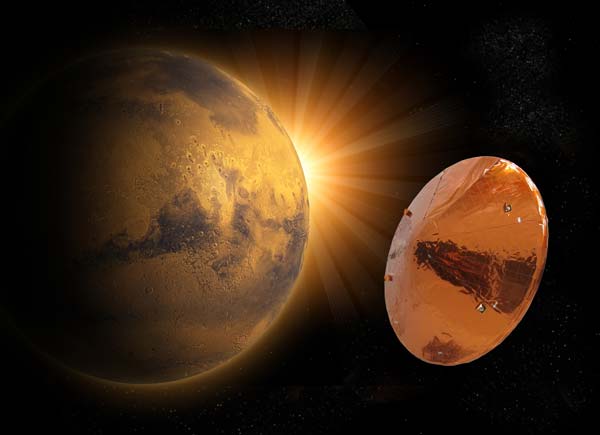
Multilayer Insulations; HPS equipped the whole EDM Module inside and outside with MLI and will land with 10kg MLI on Martian surface
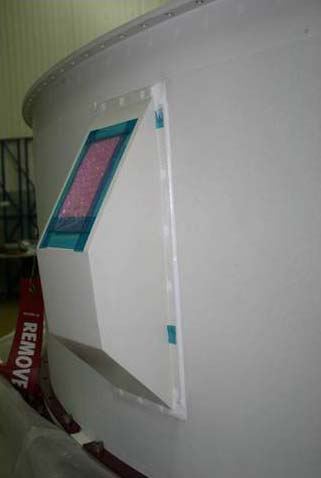
Protection of an external camera against heat from aeroflux during launch
ECM has succesfully manufactured structures and mirrors in small series up to 250 parts up to
size of 2m.
Our products increases the perfomance also for ground based optics and telescopes. Example: Large Survey Synoptics Telecope (LSST)
Berlin Space Tech has developed an integrated attitude control system for the satellite.
80 kg micro satellite carrying 3 payloads. Two hyper spectral cameras (VNIR & SWIR) and one high resolution real time video camera.
Development, Qualification and Manufacturing of the converter
The converter is based on a unique ASP-design with the effect of a high efficiency without use of ITAR-restricted parts.
The assembly line for SMD manufacturing is verified according to ECSS-Q-ST-70-38C through ESA. ASP-Equipment is enabled to manufacture PCB´s for Flight Models
RF-Communications Equipment for remote Control (256 kbps Uplink) and Video-/ Data Downlink (4 Mbps)
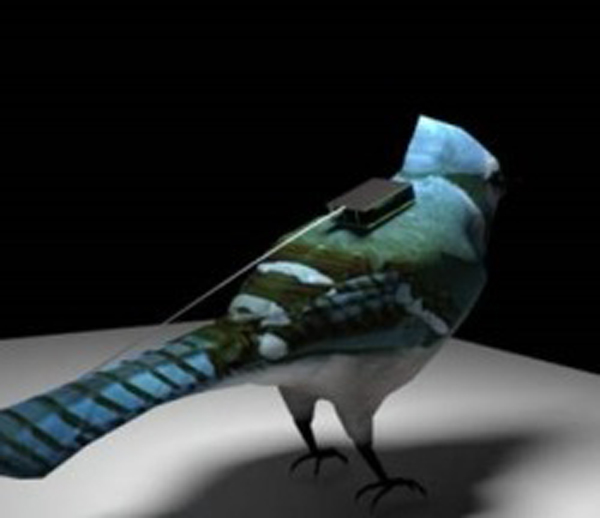
The ISS Demonstrator consists of Antennas für transmission and reception and the required electronics. The animal tag consist of an extremely light tag, including GPS, Solar array, battery and micrelectronis.
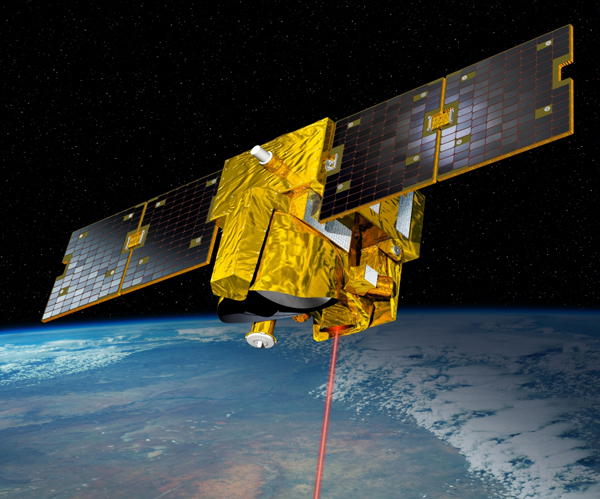
The FRU provides the frequency references for the oscillator and the optical parametrical oscillator of the pulsed laser source. It contains several diode lasers, a methane cell, a wavemeter and the associated electronics.
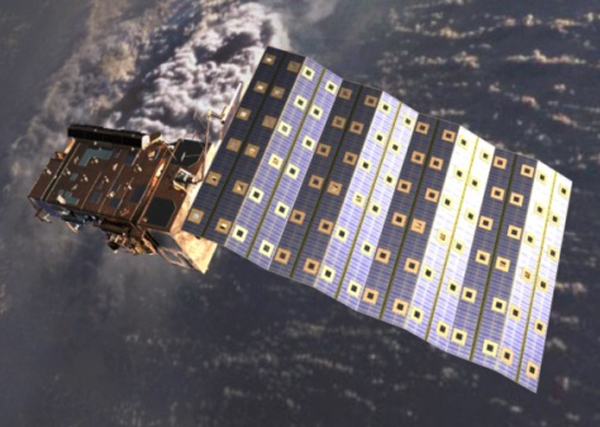
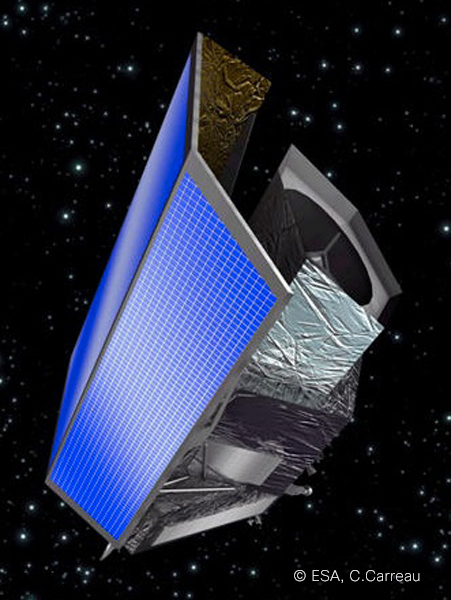
The Sunshield protects the telescope from the thermal, visible and infrared radiation of the sun and provides the required operational power.
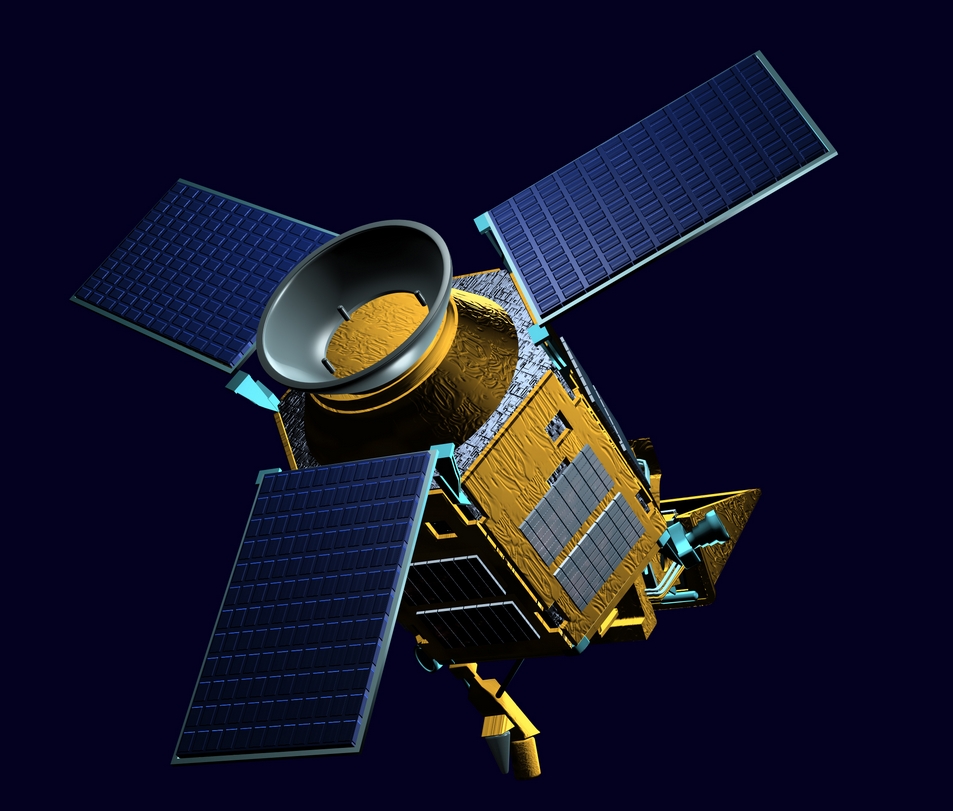
3 Solar generators with deployment mechanisms, including HDRM
Im Bereich des Optical Ground Support Equipments bietet die Astro- und Feinwerktechnik Adlershof GmbH attraktive Lösungsbausteine aus erfolgreichen Projekten zu der Gestaltung von Messplätzen.
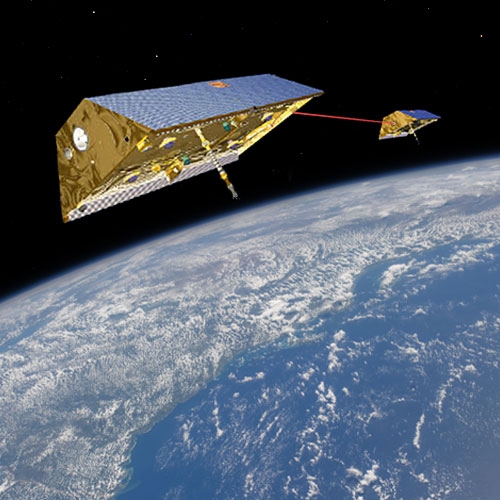
Retroreflector, Optical Bench, Instrument AIT BUS: Primary Structure, Tertiary structure, Antenna Boom, MGSE
LRI: High precission optics and highly stable optomechanics (CFRP, Zerodur, titanium) for beam shaping, routing and detection
BUS: highly stable CFRP Structures and a deployment mechanism.
As the outer segments and the complete boom fold out separately, there are only two degrees of freedom during each fold-out procedure; only three degrees of freedom in the case of spin-stabilized satellites. The design principle of the Double Star boom can be adapted to a variety of spinstabilized satellites. A concept for an active, springdriven deployment, using redundant deployment springs at the hinges is available for non-spinning satellites. Both versions can be realized either with one or two boom segments. The length of the deployed boom can be extended to more than four meters, depending on the dimensions of the spacecraft and on the mass to be deployed.
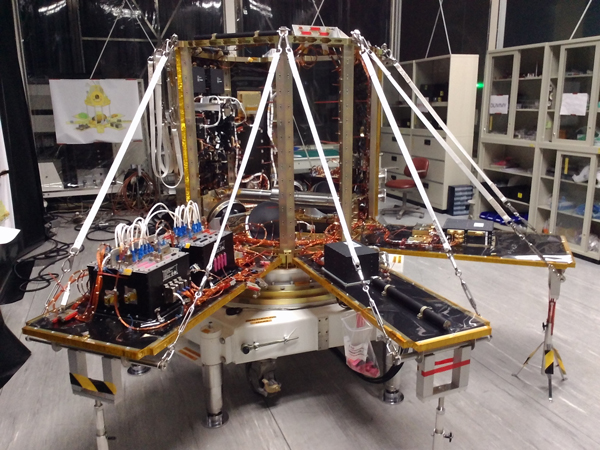
Solar generators, Coldgas propulsion system, Satellite primary structure
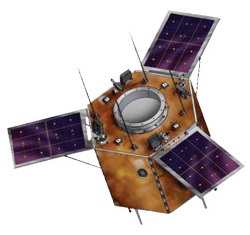
High resolution remote sensing satellite, resolution 2.5 m(PAN),5 m(MS)
Solar generators with deployment mechanisms and pyrodrive modules
- Mechanism
- Thermal control
- Energy supply
- Attitude control
- AIV of client satellite
- GSE
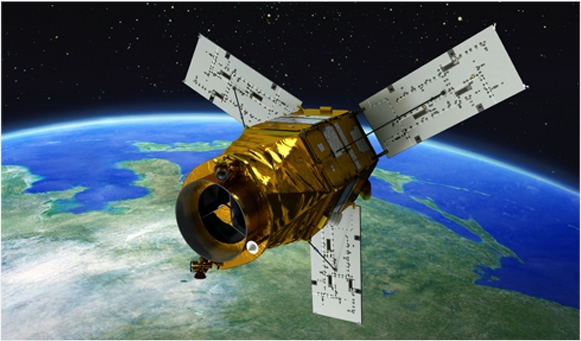
High resolution earth observation for GIS, 0.7 m GSD
The patented deployment mechanisms of the solar generators are optimized for high torque, low friction and low shock loads
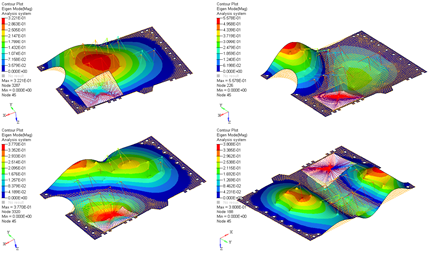
Test Prediction, -plan, -campaign and -correlation
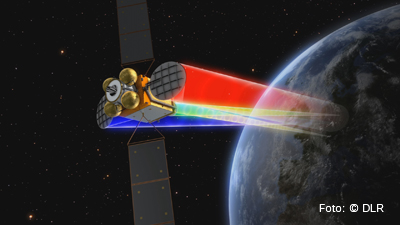
- Mechanical test planning and
on-site test lead engineering (including whole S/C)
The PTF generates the Galileo system time. We developed the Systrem Test Specification and conducted a software based system test of the PTF Oberpaffenhofen.
On-board Software for control of the IRS payload, an infrared telscope and interferometer, plus auxiliary devices
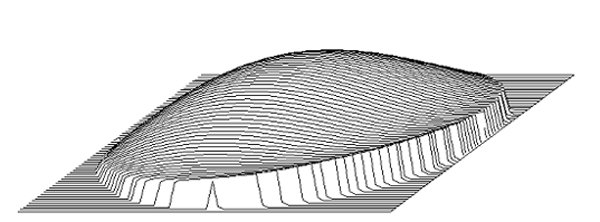
Gravity CIAO is a second generation instrument for the Very Large Telescope Interferometer (VLTI), designed to enhance the near-infrared astrometric and spectro-imaging capabilities of VLTI. KTO has analysed the optical performance of the instrument.
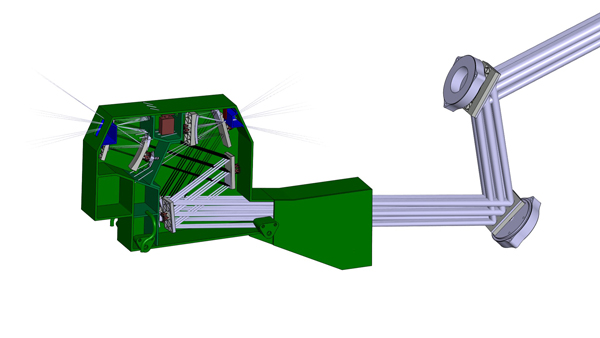
The EDM diagnostic monitors the chamber walls of the ITER fusion reactor for surface erosion and/or material deposition after plasma operations. For this non-contact in-situ surface analysis the system is relying on a dual beam speckle interferometry. KTO is responsible for the system design as well as for optical and opto-mechanical design.
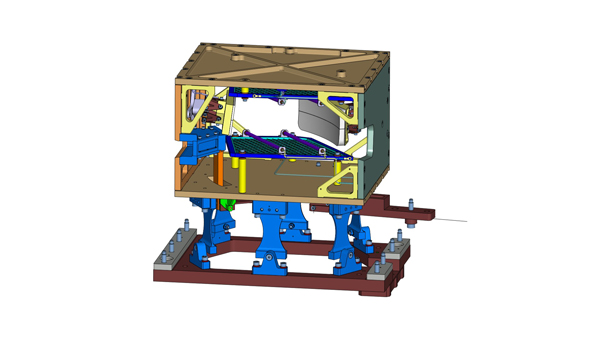
As an optical diagnostics, the H-alpha instrument measures emissions from hydrogen isotopes and impurities in the ITER fusion process. KTO is responsible for the system design as well as for optical and opto-mechanical design.
The manufacturing technologies developed for aerospace projects provide the INVENT GmbH with the means for customer-specific manufacturing of lightweight components and high performance materials that enable extreme conditions like temperature, stiffness of thermal expansion in correlation with weight minimization. Therefor weigth- and performance-optimized materials from aerospace application are employed. The corresponding processes have been developed in the scope of aerospace programmes and, thus, are available for terrestrial applications.
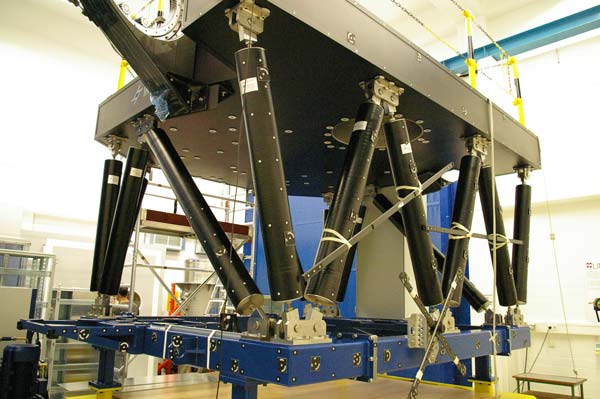
For the interferometric camera the optical bench was manufactured as large scale high precision mounting table from Aluminum/CFRP-sandwich platform and CFRP-wound struts with a maximum allowable deformation of 0.01 mm
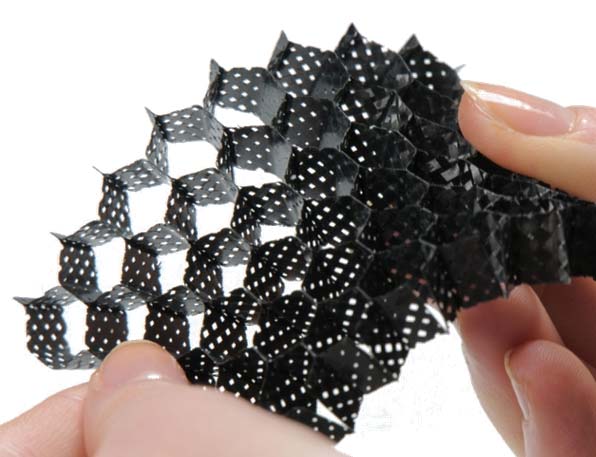
etc. are employed for the construction of particle accelerators, as the required lightweight design can be combined with low thermal expansion.
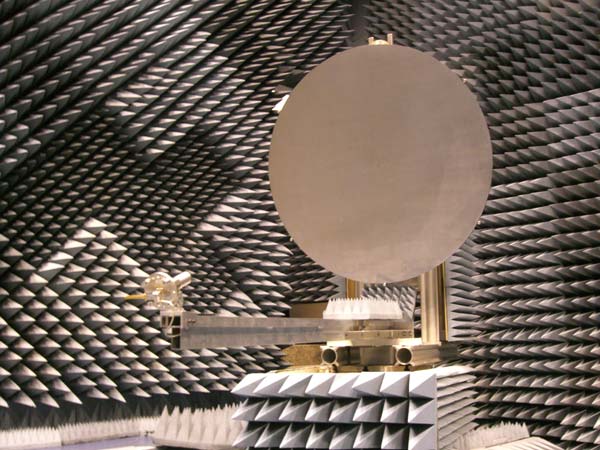
Combining latest premium materials from R&D in an optimised sandwich design enables a significant performance increase compared to traditional aluminum construction methods. CFRP/CFRP reflectors are therefore able to transmit higher data speeds at a lower antenna weight even under extreme space conditions with temperatures of +/-150°C.
STANT (2009-2011)
FLANT (2012-2015)
HISST (2009-2011)
HISST2 (2011-2012)
H2KAR (2012-2018)
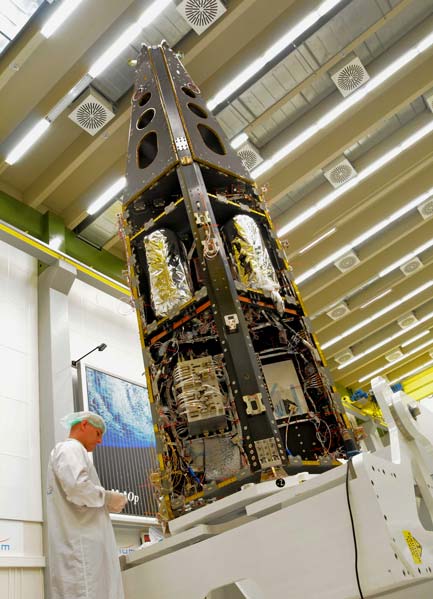
INVENT designed and manufactured magnetic torquer (air coil) frames for the SWARM satellites. Further on, thermally high conductive CFRP plates made of K13 pitch fibre were made.
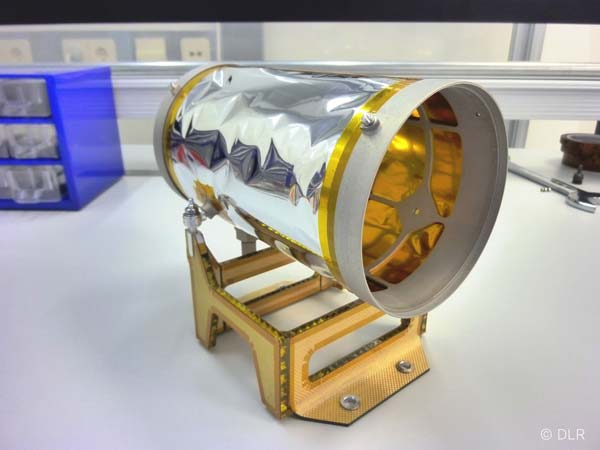
The BELA SPU, a straylight protection unit for the BepiColombo laseraltimeter, was designed, analysed and manufactured by INVENT. The key challenges for this unit were the very small dimensions, severe mass requirements and the Gold plating on CFRP sandwich parts.
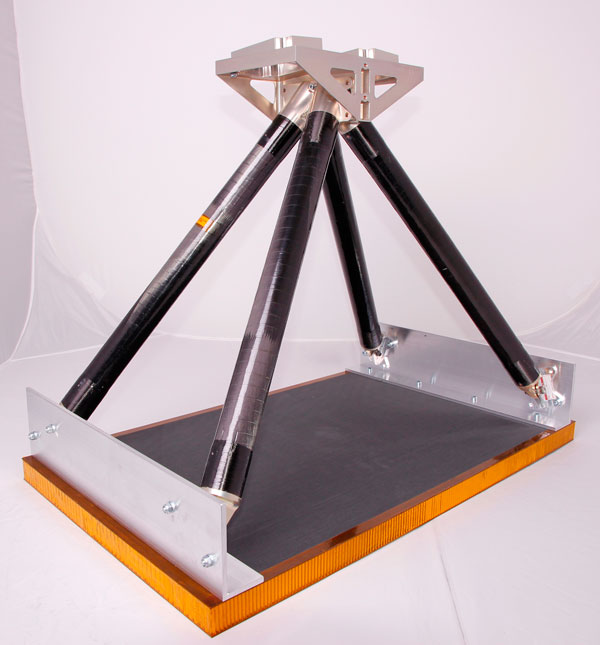
INVENT is in charge of the development and manufacturing of Meteosat Third Generation (MTG) support structures which includes the helium tank, mid thruster, reaction wheel and panel supports.
INVENT manufactured thermal plates from highly conductive CFRP (featuring K13 pitch fibre) for the GRACE-FO satellite.
INVENT manufactured Aluminum/Aluminum sandwich panels incl. all inserts for the FormoSat 5 satellite.
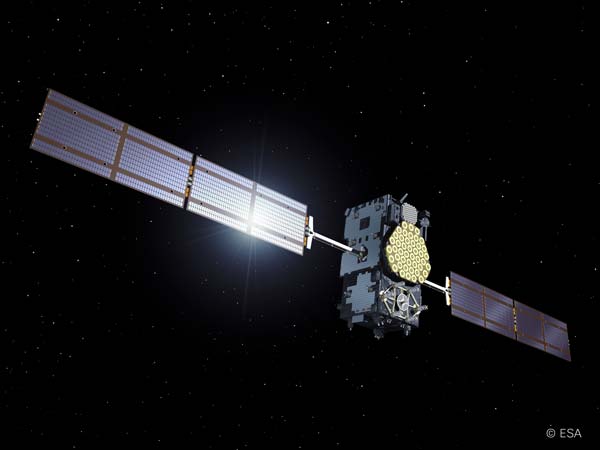
INVENT manufactured approx. 70 Aluminum/Aluminum sandwich raw panels for the first 14 Galileo satellites.
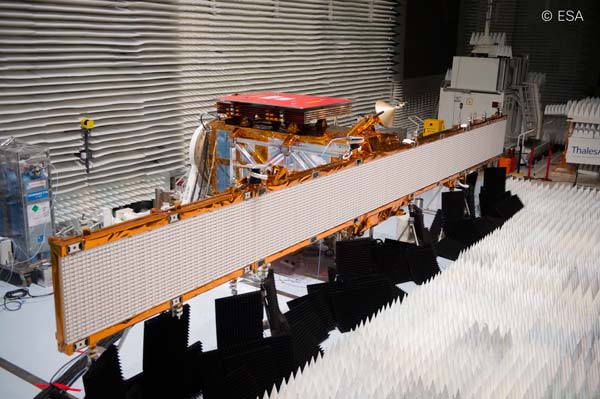
Following a 3 year development INVENT manufactures raw CFRP waveguides and thermally high conductive CFRP parts for the SAR antennas of TerraSAR-X, Tandem-X and Sentinel 1A + B since 2004. Within these projects INVENT made more than 5000 CFRP parts for several QMs and FMs.
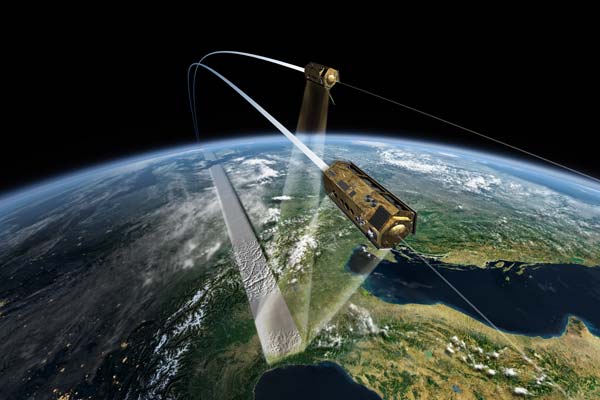
Following a 3 year development INVENT manufactures raw CFRP waveguides and thermally high conductive CFRP parts for the SAR antennas of TerraSAR-X, Tandem-X and Sentinel 1A + B since 2004. Within these projects INVENT made more than 5000 CFRP parts for several QMs and FMs.
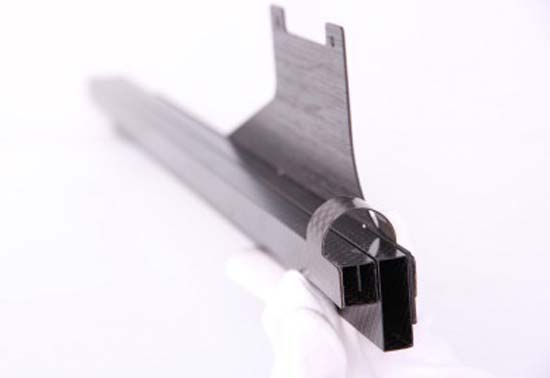
Following a 3 year development INVENT manufactures raw CFRP waveguides and thermally high conductive CFRP parts for the SAR antennas of TerraSAR-X, Tandem-X and Sentinel 1A + B since 2004. Within these projects INVENT made more than 5000 CFRP parts for several QMs and FMs.
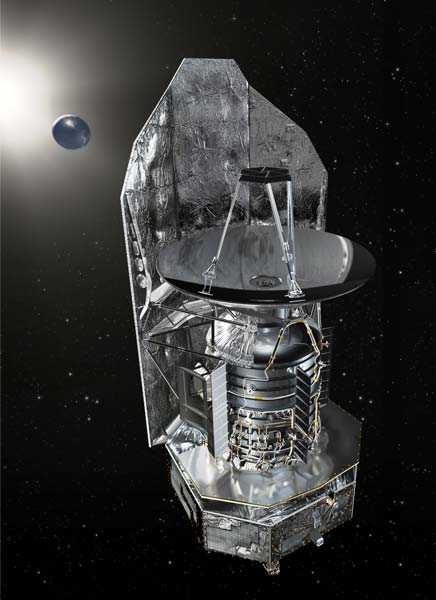
In the frame of the Herschel project INVENT developed and built mechanically high-stressed, but thermally isolating, isostatic mounts, made of CFRP & aluminum. Further on, a thermal strap out of copper and CFRP could be developed. All components work under cryogenic temperatures between 2 and 4 K.
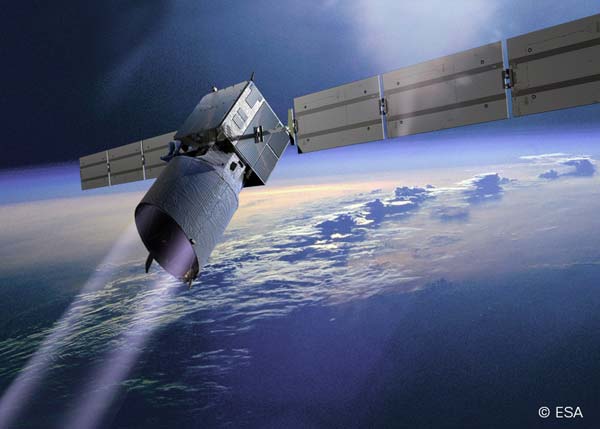
The ALADIN sun baffle consists of a CFRP strut framework. Each strut features CFRP inserts (to cover CTE mismatch) for the strut connection.
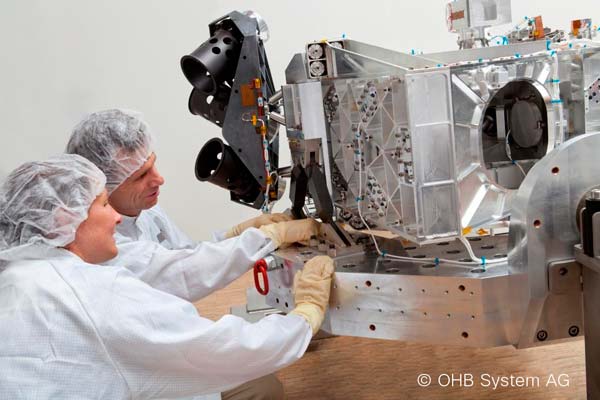
The IOU (Instrument Optical Unit) and the STSA (Star Tracker Sensor Assembly) supports were designed as CFRP/AlBeMet and Titanium/Invar bipods. The major design driver was the required mechanical performance going simultaneously with a small thermal conductivity and expansion.
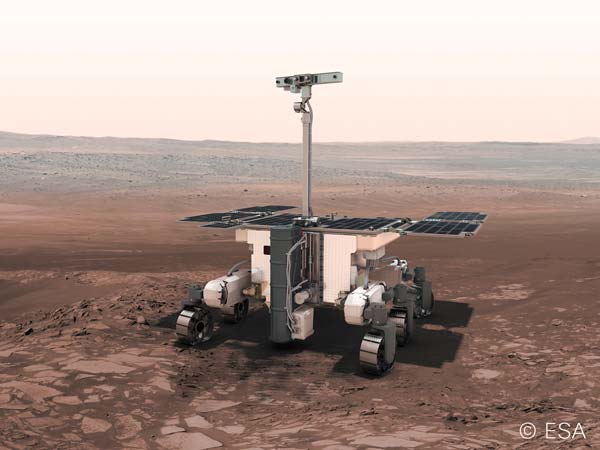
The deployable mast assembly (DMA) consists of a CFRP boom with titanium fittings, which support the Rover's stereo camera system.
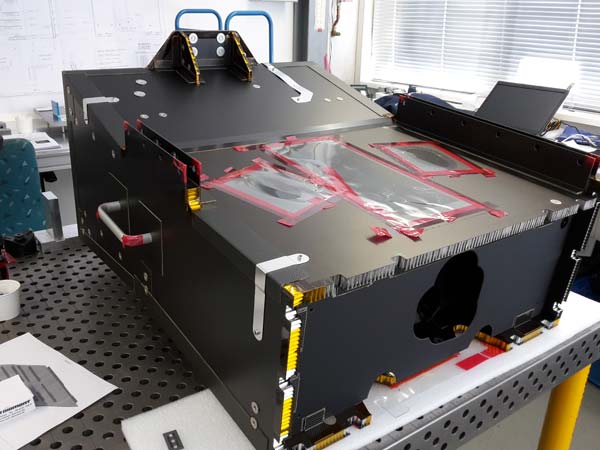
The Sentinel 4 UVN OIMS consists of CFRP sandwich panels, monolithic CFRP, GFRP and metallic parts. The Nadir Baffle (service temp. 140 °C) incl. CFRP vanes is fully bonded by adhesive. The TSA hexapod structure is made of CFRP struts incl. Titanium fittings.
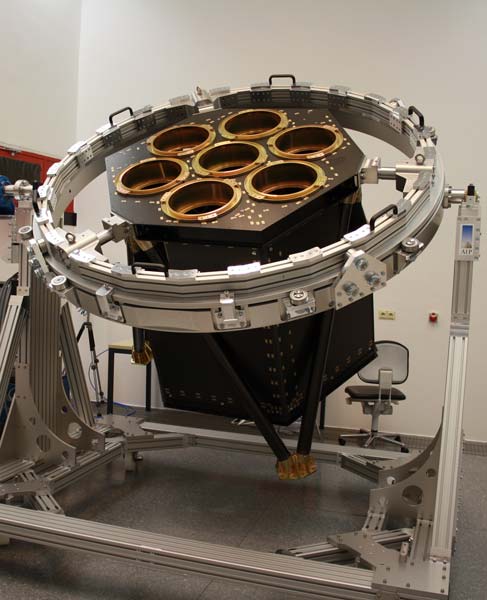
The eROSITA structure is mainly built out of adhesive bonded CFRP/Aluminum sandwich panels for the optical bench and Aluminum/Aluminum sandwich panels for radiators. Further on, CFRP struts (hexapod for opt. bench), GFRP struts for the radiator truss work and monolithic CFRP parts have been developed and assembled by INVENT.
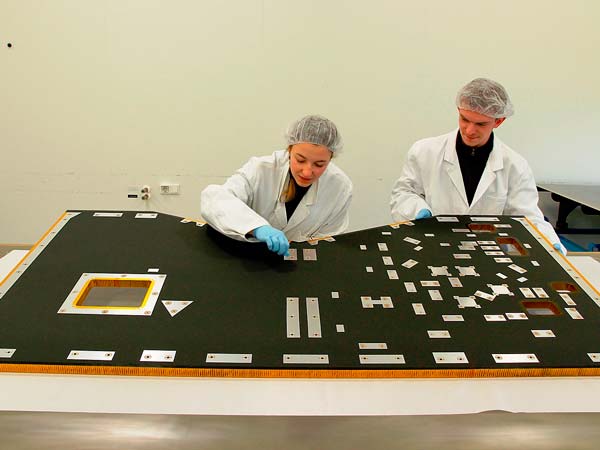
The ExoMars load-bearing structure of the orbiter mainly consists of CFRP & aluminum sandwich with
>5300 metallic inserts, heterogeneous aluminum cores, structural and thermal doublers, grounding and painting (next to the central tube - not by INVENT). Additionally various CFRP, aluminum and titanium brackets for reaction wheels, LGA, He-tanks and star trackers were developed and manufactured
MGSE Transport Container for Small Satellites / Instruments
The container system of Astro- und Feinwerktechnik Adlershof GmbH is individually suited to the size of your satellites or instruments. Our assurance of safe transportation goes without saying.
With these premises, we offer you optimal solutions for your transportation needs
- hermetically sealed inner areas
- defined gas atmospheres
- vibration-reduced transportation
- data connections for data recording during transport
- adapters for transport systems (Euro / ISO pallets, lifts)
As the outer segments and the complete boom fold out separately, there are only two degrees of freedom during each fold-out procedure; only three degrees of freedom in the case of spin-stabilized satellites.
The design principle of the Double Star boom can be adapted to a variety of spinstabilized satellites. A concept for an active, springdriven deployment, using redundant deployment springs at the hinges is available for non-spinning satellites.
Both versions can be realized either with one or two boom segments. The length of the deployed boom can be extended to more than four meters, depending on the dimensions of the spacecraft and on the mass to be deployed.
a panel structure consisting of 3 panels, development of a fold-out system with four exact constructional replicas and completely independent solar panels for small satellites
The ACS Test Facility includes:
- air bearing table with a platform allowing free 360° rotation around the vertical axis and between 20° and 30° around the horizontal axes
- high precision in-orbit earth magnetic field simulation
- electronic center of gravity (CoG) calibration
- adjustable and movable sun simulation
- WLAN command line
- safety mechanisms for save operation and satellite mounting
- power supply and distributio
the primary payload and other satellites to be launched. After the safe transportation of the device into the orbit, a deployment with a high reliability and a low spin rate is achieved by patented design principles. After a successful deployment, a telemetry signal is available for the launch provider.
The family of CubSat Deployer consists of the Single Picosatellite Launcher (SPL), the Double Picosatellite Launcher (DPL) and the Triple Picosatellite Launcher (TPL). The SPL is used to deploy one 1U CubeSat. The DPL is used to deploy one 2U CubeSat or two 1U CubeSats etc. The product line relies on a modular and redundant design
It is designed especially for small satellite applications. Outstanding features are low mass and size as well as the low energy consumption. The ASG-1 measures angular increments in three orthogonal axes. Using these angular increments, the rotation speed of the satellite and the relative position of the satellite in relation to a starting point are calculated.
reaching from the world's smallest commercial reaction wheel RW 1 (10-4 Nms) to the RW 250 (4 Nms). The reaction wheels RW 90 and RW 1 are already flight proven. Four reaction wheels RW 90 come into operation at the small satellite TET-1 (launch in 2012). State of the art feedback systems in combination with model based controller algorithms making smart reaction wheels the ideal solution for zero-momentum attitude control strategies because these reaction wheels will operate with high accuracy as well in the "low wheel speed region". Astro- und Feinwerktechnik Adlershof GmbH
Test bed for rotational speed sensors. The test bed allows new combinations of measuring tasks. Therefore the sensors can be checked under different application scenarios.
Main functions:
• wide speed range
• high temperature loads
• Rotational vibrations of the code wheel
• maximum air gap
• air gap jumps
• free positioning of the sensors in four axes in relation to the code wheel
Microjet, developed by AIG (Aerospace Innovation GmbH) of Berlin, is a modularly designed propulsion system for Nanosatellites and Microsatellites based on the gas-resistojet-concept. It consists of a PST (Pressure Tank Unit) with nitrogen which is filled or drained, respectively, through a FDU (Fill and Drain), a FCU (Flow Control Unit) responsible for the control of correct propellant mass flow, as well as one or more THUs (Thruster Units). Each of these THUs contains a pulse valve and a nozzle for the actual thrust generation. Additionally, according to the definition of the Resistojet-concept, an electrical resistance-heating element might be applied for higher performance demands. The entire propulsion system is controlled by the PCU (Propulsion Control Unit), which can also be resigned of, if the satellite itself is capable to control the Microjet propulsion subsystems.
Aquajet is a small satellite propulsion system designed and developed at AI (Aerospace Innovation GmbH), Berlin. The objective is on-orbit qualification/verification of the Aquajet system performance on the TET-1 mission. The Aquajet micropropulsion device is an enabling system, small enough to provide its services to future pico- and nanosatellite missions. In particular, the micropropulsion device is an enabler for the positional control of nanosatellite constellations.
instrument for infrared spectroscopy; informations about the nature of atmosphere
WAOSS stereo camera (Wide-Angle Optoelectronic Stereo Scanner) global topographical mapping with good ground resolution.
Das EGSE dient der Integration und Inbetriebnahme sowie dem Test eines Satelliten bzw. der Satellitenkomponenten.
Die Aufgaben eines EGSE umfassen:
◾Energieversorgung des Satelliten
◾Erfassung, Darstellung und Archivierung von Messwerten
◾Senden von Telekommandos
◾Empfang von Telemetrie
◾Telemetrie-Verarbeitung, Interpretation, Darstellung und Archivierung
◾Entwicklung, Validierung und Ausführung von (Flug-)Prozeduren