RUAG Space | Media Relations | Schaffhauserstrasse 580 | 8052 Zurich | Switzerland | www.ruag.com
Media Release
Zurich, July 14, 2021
Strategic Partnership Moves into the Next Round
With the signing of the contract for the 5 th modification of the development and production contract (“Mod5) for the Atlas as well as Vulcan Centaur rocket
programs, United Launch Alliance (ULA) and RUAG Space extend and expand their successful cooperation.
In 2015, United Launch Alliance (ULA) announced a strategic partnership with RUAG Space to produce composite structures for the Atlas V rocket in the USA. The move was part of the transition from the Delta and Atlas rocket programs to the next generation of launch vehicles, the Vulcan family. The Vulcan Centaur launch vehicle will be used for both satellite launches and manned missions.
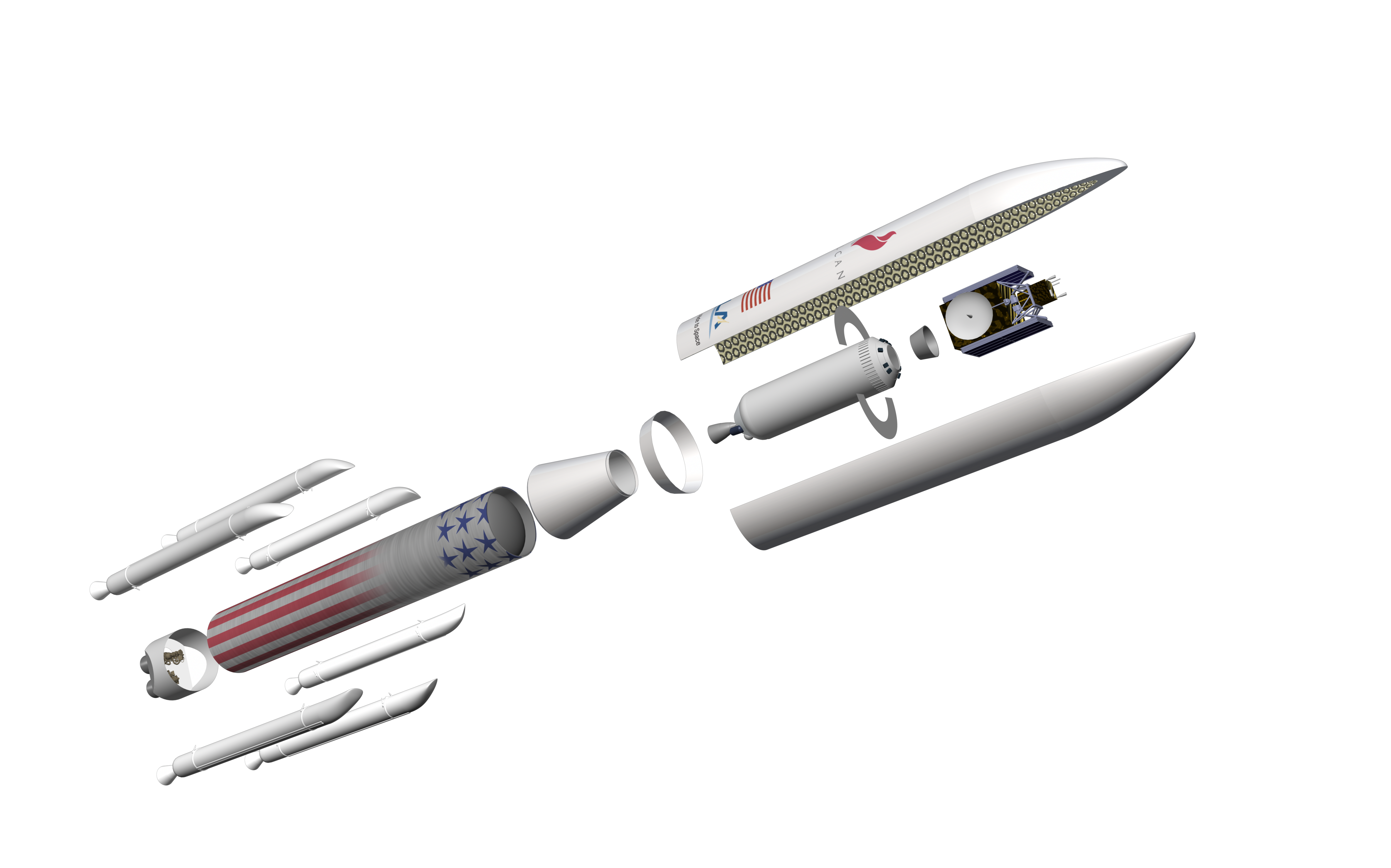
ULA_Vulcan
Over 120 successful ULA launches with RUAG Space products
As part of the strategic partnership, RUAG Space had set up shop in Decatur (US state of Alabama) in a 130,000-square-foot ULA building originally used for the Delta program and, following successful conversion, began operations in 2017. Until 2017, the structures were produced at RUAG Space’s sites in Zurich and Emmen, Switzerland. The last structure
manufactured in Emmen for the Atlas launch vehicle left Switzerland for the USA at the end of September 2020 on board an Antonov An-124. Now production is taking place directly on site in Decatur, where RUAG Space will also manufacture the carbon fiber structures for the new Vulcan launch vehicle in the future following the successful development and qualification. The payload fairings in composite technology – consisting of two half-shells that are mechanically joined together – are manufactured in a modern, partially automated process. RUAG Space’s payload fairings use a sandwich architecture of aluminum honeycomb material sandwiched between an inner and outer cover layer of woven carbon fiber. A cork layer applied to the exterior provides thermal protection against frictional heat generated during launch. Thanks to an innovative process, the carbon fiber structures required for the payload fairing can be manufactured without the use of an autoclave and thus more cost-effectively than in the conventional process.
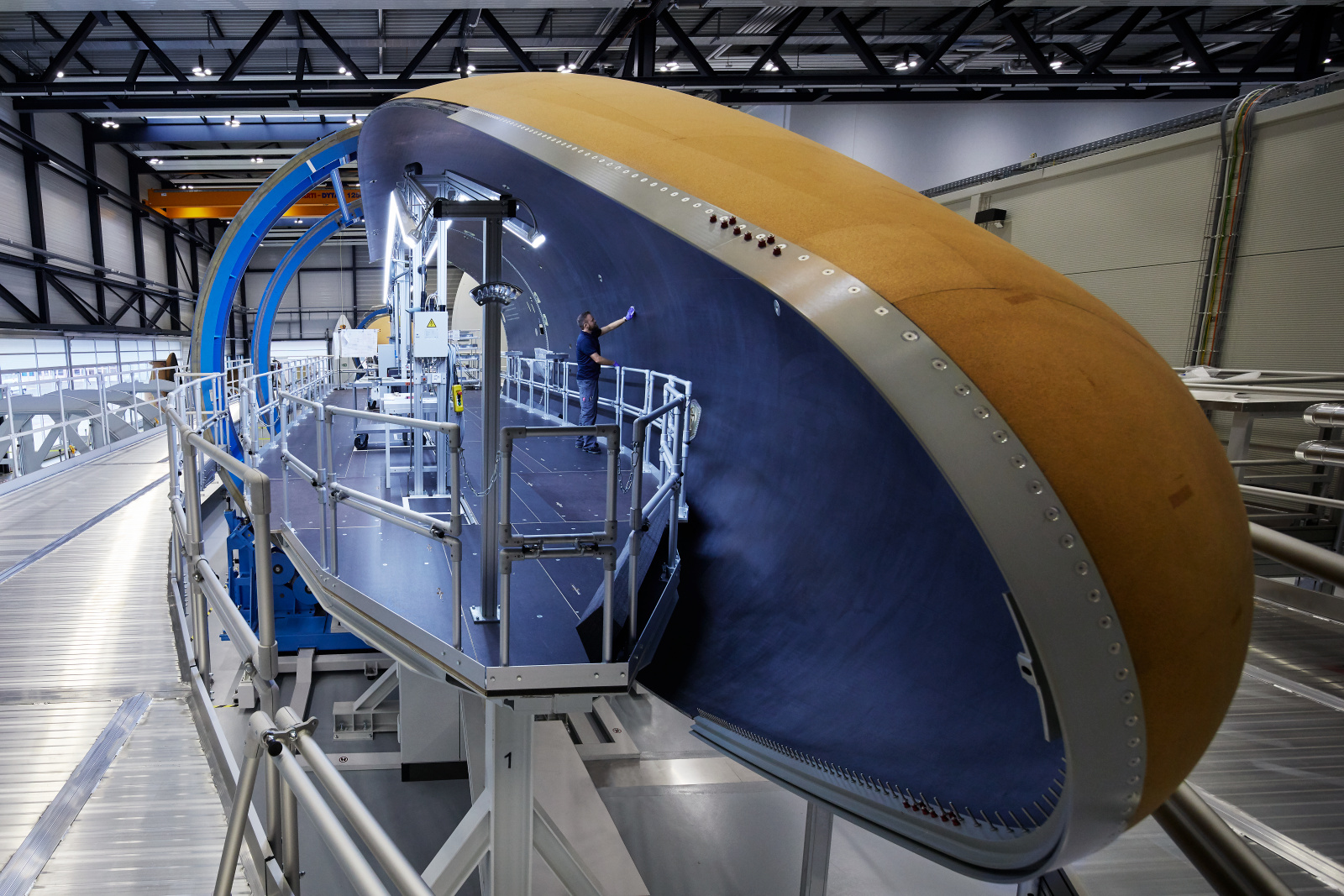
RUAG Space
The Decatur facility currently supplies carbon fiber composite structures for ULA’s Atlas launch vehicles, including the payload fairing for the Atlas V-500 launch vehicle and the interstage adapter for the Atlas V-400, as well as carbon fiber structures for qualification and future production of the new Vulcan launch vehicle, including payload fairings, interstage adapters and heat shields. Since the beginning of the strategic partnership between ULA and RUAG Space, more than 120 successful rocket launches have been carried out by ULA using RUAG Space products.
Cooperation extended and expanded
With the signing of the modification of the production contract (“Mod5”) between ULA and RUAG Space now completed, the successful cooperation enters the next round. While the production of the Atlas rocket and the development and qualification of the Vulcan components have been the focus so far, “Mod5” refers to orders until 2024. The additional order volume for RUAG Space from the contract modification amounts to 110 million Swiss francs. Holger Wentscher, who heads the Launchers product group at RUAG Space, says: “I would like to express my sincere thanks to ULA for the trust placed in us and for the cooperative partnership. With my colleagues at our Decatur facility, I look forward to continuing our shared success story.”
“The partnership between ULA and RUAG has been a vital part of our successes over the many years,“ says Daniel Caughran, ULA vice president of Productions, Operations and Supply Chain. “The recent contract modification reflects the ongoing trust and commitment to the partnership with RUAG Space as we proceed towards the first launch, and many future launches, of the Vulcan Centaur.”
This media release can be found here: https://www.ruag.com/news
RUAG International
Point of Contact: Philipp Bircher, Director Communications Space,
Phone: +41 79 790 11 8
Email: philipp.bircher@ruag.com
RUAG Space is the leading supplier to the space industry in Europe with a growing presence in the USA. Around 1,300 employees in six countries develop and manufacture products for satellites and launch vehicles – giving RUAG Space a central role in both the institutional and commercial space markets. RUAG International is a Swiss technology group with production sites in 14 countries and is divided into four divisions: Space, Aerostructures, MRO International and Ammotec. RUAG International employs around 6,500 people, of whom around two thirds work outside Switzerland. www.ruag.com